What is Porosity in Welding: Important Tips for Getting Flawless Welds
Deciphering the Enigma of Porosity in Welding: Tips for Reducing Issues and Making Best Use Of Quality
In the elaborate globe of welding, porosity stays a persistent obstacle that can considerably influence the quality and honesty of bonded joints. Recognizing the aspects that add to porosity formation is crucial in the quest of remarkable welds. By deciphering the enigma of porosity and implementing efficient approaches for defect minimization, welders can raise the criteria of their job to achieve exceptional high quality outcomes. As we look into the depths of porosity in welding, revealing the secrets to its prevention and control will be paramount for experts looking for to grasp the art of high-quality weldments.
Understanding Porosity in Welding
Porosity in welding, an usual issue encountered by welders, describes the presence of gas pockets or spaces in the welded product, which can compromise the integrity and high quality of the weld. These gas pockets are commonly caught throughout the welding procedure because of various aspects such as incorrect shielding gas, polluted base products, or wrong welding criteria. The formation of porosity can damage the weld, making it prone to breaking and rust, eventually leading to architectural failures.
By recognizing the relevance of keeping proper gas protecting, ensuring the tidiness of base products, and maximizing welding settings, welders can substantially lower the possibility of porosity formation. In general, a detailed understanding of porosity in welding is important for welders to generate premium and long lasting welds.

Typical Reasons For Porosity
When checking welding procedures for potential top quality concerns, understanding the typical reasons for porosity is crucial for maintaining weld integrity and stopping architectural failings. Porosity, identified by the presence of cavities or spaces in the weld steel, can significantly compromise the mechanical buildings of a bonded joint. One usual source of porosity is improper shielding gas coverage. Inadequate shielding gas flow rates or improper gas mixtures can lead to atmospheric contamination, resulting in porosity development.
Additionally, welding at inappropriate parameters, such as exceedingly high travel rates or currents, can generate extreme turbulence in the weld pool, trapping gases and triggering porosity. By addressing these typical reasons with proper gas protecting, material preparation, and adherence to optimum welding parameters, welders can lessen porosity and enhance the high quality of their welds.
Strategies for Porosity Prevention
Applying effective safety nets is vital in minimizing the incident of porosity in welding processes. One method for porosity avoidance is guaranteeing proper cleansing of the base steel before welding. Pollutants such as oil, oil, rust, and paint can bring about porosity, so extensive cleansing using ideal solvents or mechanical methods is vital.

An additional trick safety net is the selection of the appropriate welding consumables. Using top quality filler products and protecting gases that appropriate for the base steel and welding procedure can significantly decrease the danger of porosity. Furthermore, keeping correct welding criteria, such as voltage, existing, take a trip rate, and gas circulation price, is essential for porosity avoidance. Deviating from the recommended setups can result in inappropriate gas coverage and inadequate blend, leading to porosity.
Moreover, utilizing proper welding techniques, such as keeping a regular traveling speed, electrode angle, and arc size, can assist avoid porosity (What is Porosity). Sufficient training of welders to guarantee they adhere to finest practices and top quality control treatments is likewise important in minimizing porosity issues in welding
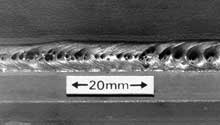
Ideal Practices for High Quality Welds
Guaranteeing adherence to industry criteria and correct weld joint preparation are fundamental facets of accomplishing regularly high-quality welds. Along with these foundational steps, there are numerous finest practices that welders can apply to even more enhance the top quality of their welds. One key technique is preserving proper sanitation in the welding area. Impurities such as oil, grease, corrosion, and paint can negatively affect the high quality of content the weld, leading to issues. Thoroughly cleansing the workpiece and bordering area prior to welding can assist mitigate these problems.
Another finest technique is to thoroughly pick the appropriate welding specifications for the article source details materials being signed up with. This consists of setting the right voltage, current, travel rate, and securing gas flow price. Correct parameter option ensures ideal weld penetration, combination, and overall top quality. Additionally, using high-grade welding consumables, such as electrodes and filler metals, can significantly impact the final weld top quality. Purchasing premium consumables can cause more powerful, more durable welds with less issues. By adhering to these finest practices, welders can continually produce premium welds that fulfill sector criteria and go beyond consumer assumptions.
Importance of Porosity Control
Porosity control plays an essential role in ensuring the honesty and high quality of welding joints. Porosity, defined by the presence of dental caries or gaps within the weld metal, can significantly endanger the mechanical properties and architectural stability of the weld. Excessive porosity weakens the weld, making it a lot more vulnerable to cracking, deterioration, and about his general failing under operational loads.
Effective porosity control is necessary for preserving the wanted mechanical homes, such as strength, ductility, and durability, of the bonded joint. What is Porosity. By reducing porosity, welders can boost the general top quality and reliability of the weld, making sure that it fulfills the performance demands of the intended application
Additionally, porosity control is crucial for attaining the desired aesthetic look of the weld. Excessive porosity not only deteriorates the weld yet also detracts from its aesthetic appeal, which can be important in sectors where looks are essential. Appropriate porosity control strategies, such as using the appropriate shielding gas, controlling the welding specifications, and making sure correct cleanliness of the base materials, are vital for generating high-grade welds with minimal flaws.

Conclusion
In verdict, porosity in welding is an usual flaw that can jeopardize the top quality of the weld. It is necessary to regulate porosity in welding to make certain the integrity and stamina of the final product.